1.What is a subconn watertight connector
Subconn waterproof connectors are electrical connectors designed specifically for underwater and extreme environments, commonly used in submersibles, marine equipment, and other applications that require waterproof protection. They use high-strength materials and sealing technology to ensure reliable connections under underwater or humid conditions, preventing moisture from entering and damaging the equipment. The characteristics of these connectors include corrosion resistance, high pressure resistance, and high reliability, making them suitable for various industrial and marine fields.
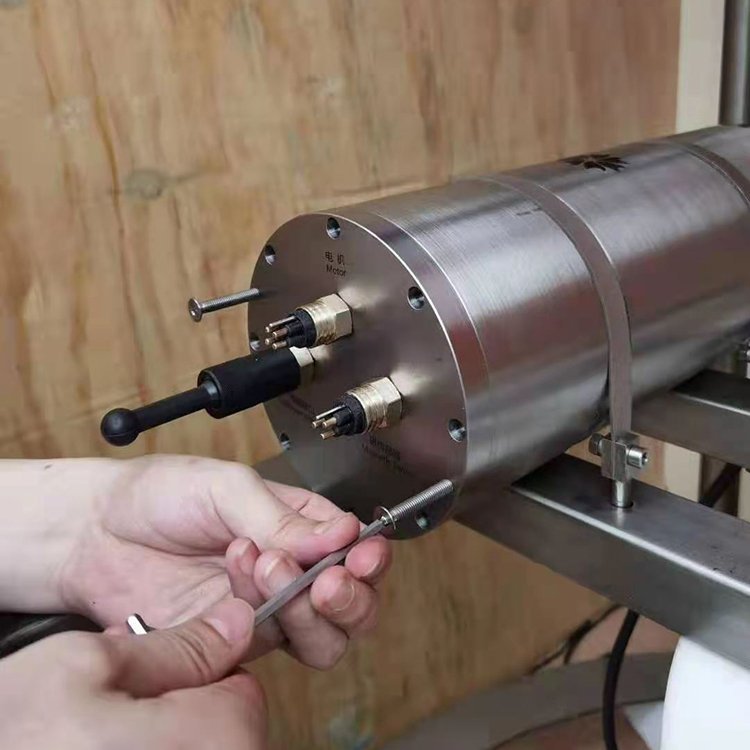
2.Key characteristics of Subcon connectors
Materials and Design
The base adopts O-ring and threaded design, made of stainless steel or sea copper material, and the cables are made of polyurethane or rubber material, all of which are seawater specific materials, ensuring pressure resistance, water tightness, and preventing seawater corrosion
Sealing performance
We use our own testing equipment to detect waterproofing, which can achieve a compressive strength of 10000 meters underwater
3.Application areas of Subcon waterproof connectors
oceanographic engineering
In the field of ocean engineering, Subconn watertight connectors are widely used in deep-sea probes, submersibles, underwater sensors, and mining equipment. These devices often need to operate in high-pressure, low-temperature, and humid environments. Subconn’s connectors ensure stability in extreme environments and prevent equipment failure caused by moisture ingress. Its waterproof performance and high pressure resistance enable deep-sea exploration missions to proceed smoothly, improving the efficiency of marine research and resource development.
Military and Defense
Military equipment typically needs to be operated in harsh environments such as underwater, desert, or extremely cold regions. Subconn’s watertight connectors are used in submarines, drones, military communication systems, and other defense equipment. Its high durability and reliability ensure the stability of military equipment in complex environments, reduce the risk of equipment failure, and improve combat effectiveness.
Industrial automation
Industrial automation equipment typically operates in harsh environments such as humidity, corrosion, and mechanical shock. Subconn’s watertight connectors are capable of maintaining the normal operation of equipment under these conditions. They are widely used in robots, sensors, control systems, and production line equipment, improving production efficiency and equipment lifespan. Its reliable performance reduces maintenance requirements and improves the stability of industrial production.
4.Guidelines for Choosing Subcon Waterproof Connectors
Connector type
Subconn’s product Divided into base and plug, such as micro 2-core, we divide it into MCBH2M+MCIL2F or MCBH2F+MCIL2M.line includes different types of connectors such as plugs, sockets, adapters, etc. Select the appropriate connector type based on the actual application requirements. For example, in applications that require high-density connections, it may be necessary to choose connectors with multiple pins, while in scenarios that require quick disconnect, quick disconnect connectors can be chosen.
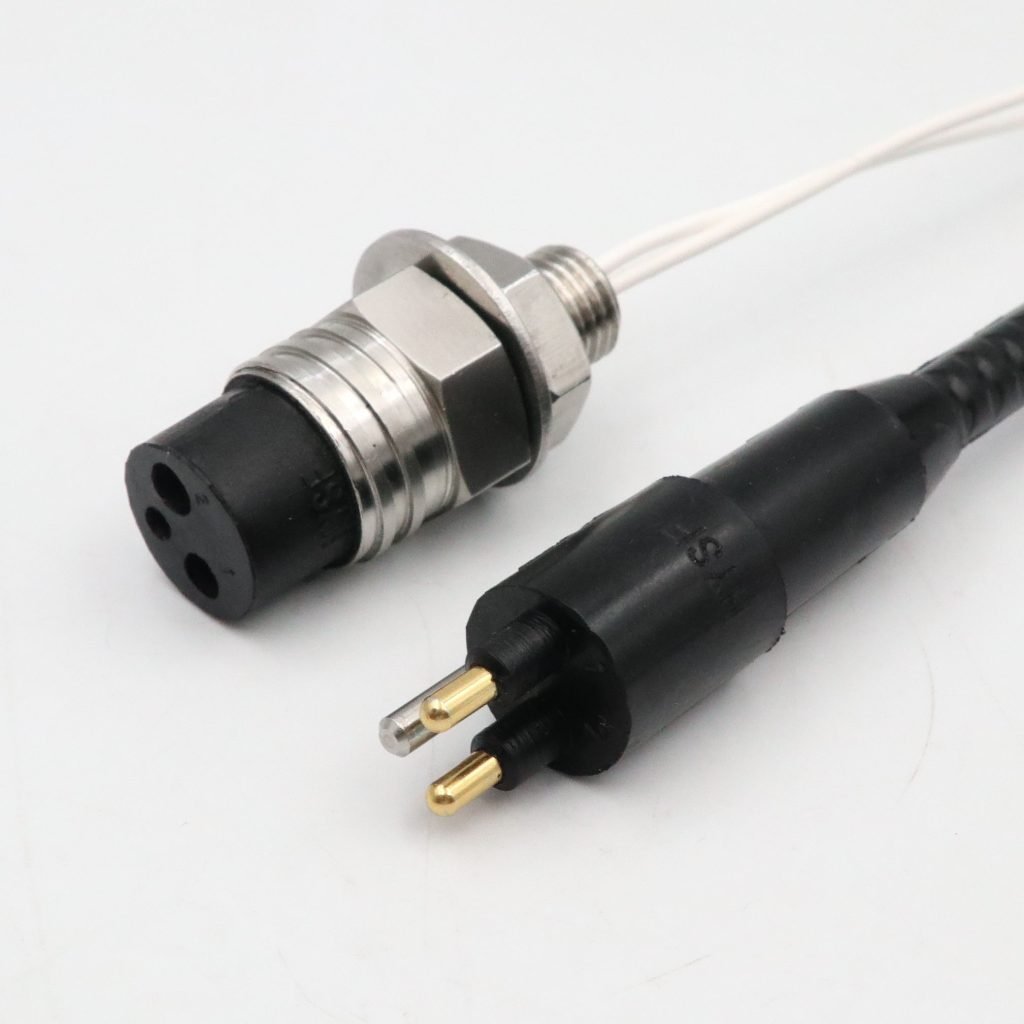
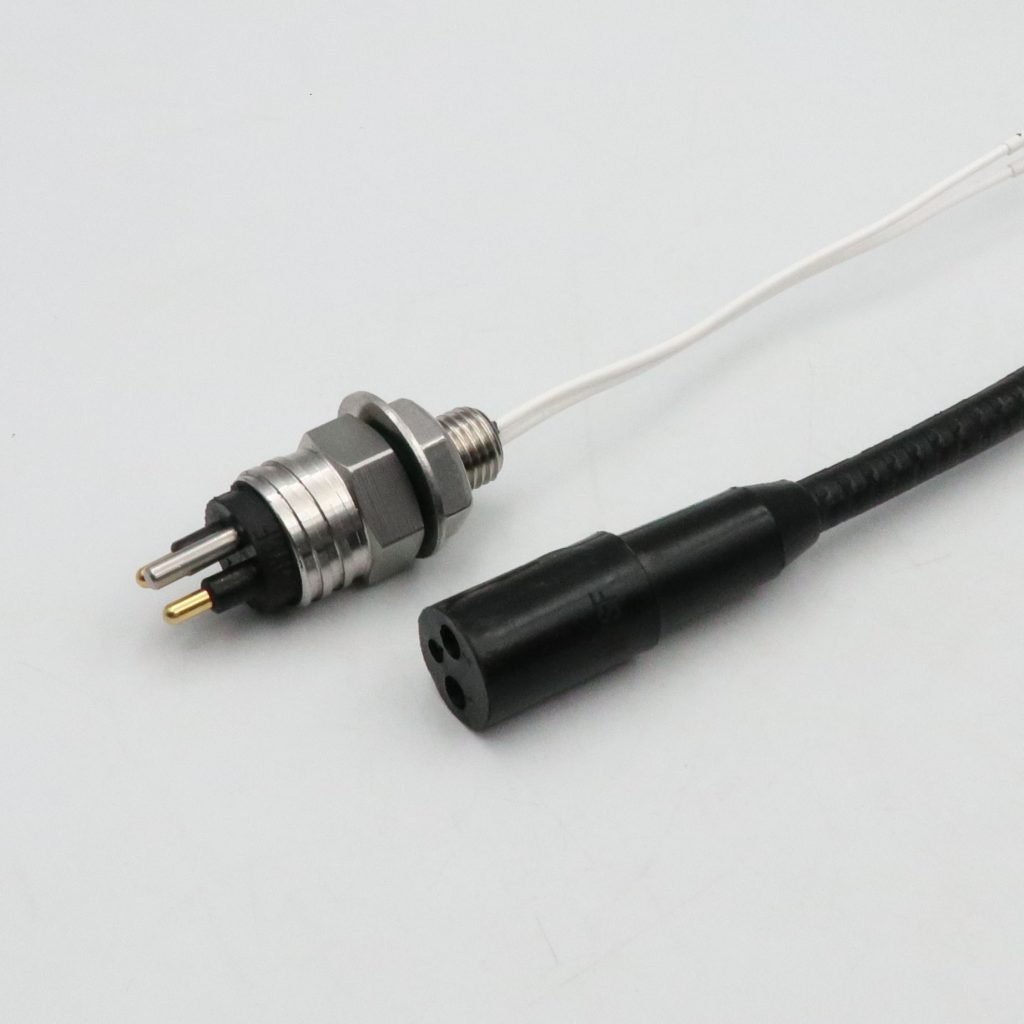
Installation requirements
Different types of connectors may have different installation requirements. For example, the MCBH2-8 hole thread is 7/16-20UNF, and the MCBH10-16 hole thread is 1/2-20UNF. When selecting connectors, it is necessary to consider whether their installation methods meet actual needs. Subconn provides detailed installation guidelines to ensure that the connector can be installed correctly and maintained in good working condition.
MCBH Dimensional Drawing
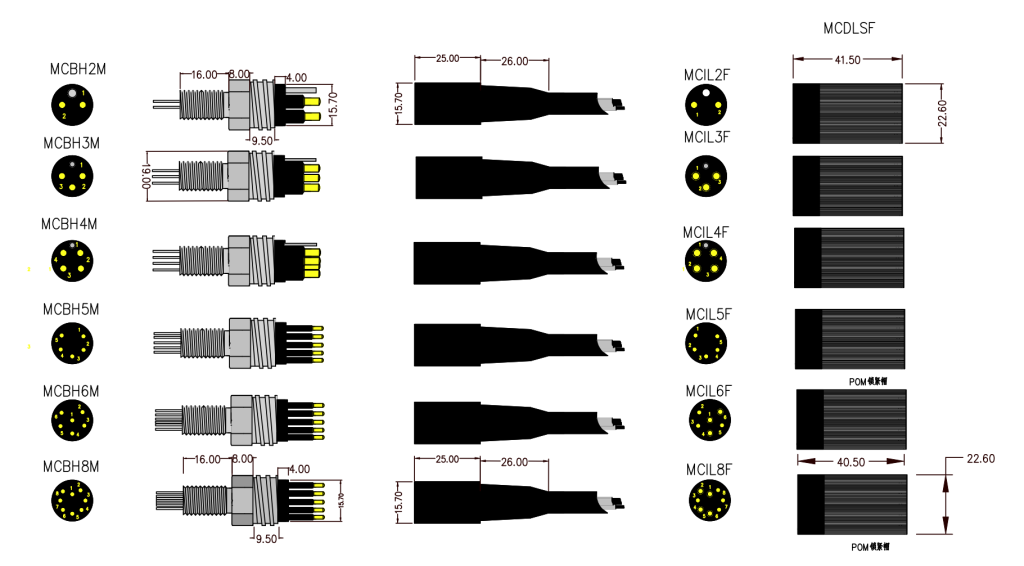
5.Installation and maintenance of Subcon watertight connectors
Installation precautions
1.Clean surface: Before installing the connector, ensure that the contact surface of the connector and the surface of the accessory are clean and free of dirt. Dirt and dust may affect the sealing performance of the connector.
2.Correct docking: When docking connectors, ensure proper alignment to avoid pin bending or damage. Follow the installation guide provided by the manufacturer to ensure the correct installation of the connector.
3.Tightening bolts: Ensure that the bolts or fasteners of the connector are securely fastened in place to avoid moisture intrusion or poor connection caused by looseness.
Maintenance suggestions
1.Regular inspection: Regularly check the sealing status and appearance of the connector to ensure that it is not damaged or aged. Regularly conduct waterproof tests to check if the connector can still maintain good waterproof performance.
2.Cleaning and maintenance: If there is dirt or salt on the surface of the connector, appropriate cleaning agents and tools should be used for cleaning. Avoid using highly corrosive chemicals to prevent damage to the casing or sealing material of the connector.
3.Replace components: If any signs of damage or poor sealing are found in the connector, replace the relevant components or the entire connector in a timely manner. Ensure that the equipment can continue to operate normally and avoid potential failure risks.
Please feel free to contact us at any time, we will communicate with you at any time